Высоколегированная сталь
Автор: Волков Семён
Дата публикации: 25 Апреля 2024
Стали, обладающие высоколегированным составом, представляют собой сплавы, в составе которых весовое содержание легирующих компонентов превосходит 10%.
Не только специфические атрибуты, которые дают добавки, отличают их, но и сложная кристаллическая структура. Для обеспечения того, чтобы каждый химический элемент занимал свое место в молекулярном решете, сначала очищают расплав от посторонних элементов и углерода. В материале присутствуют различные металлы, интерметаллиды и карбидные включения. Чтобы сформировать единую, крепкую структуру, полуфабрикаты подвергаются тепловой обработке.
По нормативам ГОСТ 5632-72, срок действия нормативного документа ограничен и высоколегированные стали подразделяются в соответствии с компонентом, который является основным.
- Никелевые: это прочный раствор хрома и добавок, находящийся в никелевой основе.
- Основой железоникелевых сплавов является железо, прочность которого увеличивается за счет добавления никеля.
Процентное содержание железа во всех видов продукции не опускается ниже 45%, в то время как концентрация основного элемена легирования начинается от 8%. Сводные характеристики таковы:
- Устойчивость к различным формам коррозии в сложных условиях использования;
- Технологические свойства: гибкость, возможность обработки методами штамповки и резки.
- Свойства материала изменяются в процессе термической обработки, когда достигаются определенные температурные пределы.
- Не все обладают свойством немагнитности: это дает возможность использовать их в процессе создания точных приборов.
Все металлические смеси подходят для сварки, но эти работы может осуществить лишь квалифицированный специалист. В процессе нагрева и плавления кромок происходит процесс рекристаллизации, окисление углерода, изменяются характеристики прочности и прочие свойства. Каждый тип сплава предназначен для своих задач, а их свойства определяются процентным содержанием легирующих элементов. Так, вольфрам и молибден используются как упрочнители в хром-никелевых системах, ванадий и марганец улучшают износостойкость, а цинк действует в роли стабилизатора благодаря своей способности устанавливать связи с множеством материалов.
Главные секторы, где используется сталь: добыча и переработка нефти, газовая промышленность, энергетика, кораблестроение, а также промышленные площадки, где применяются печи и охлаждающие устройства. В прочих сферах стали с сложным химическим составом используются не так часто. Для выполнения обычных технических функций не требуются специфические свойства стали, однако некоторые сорта применяются в быту, например, в производстве посуды, ножей или барабанов для стиральных машин.
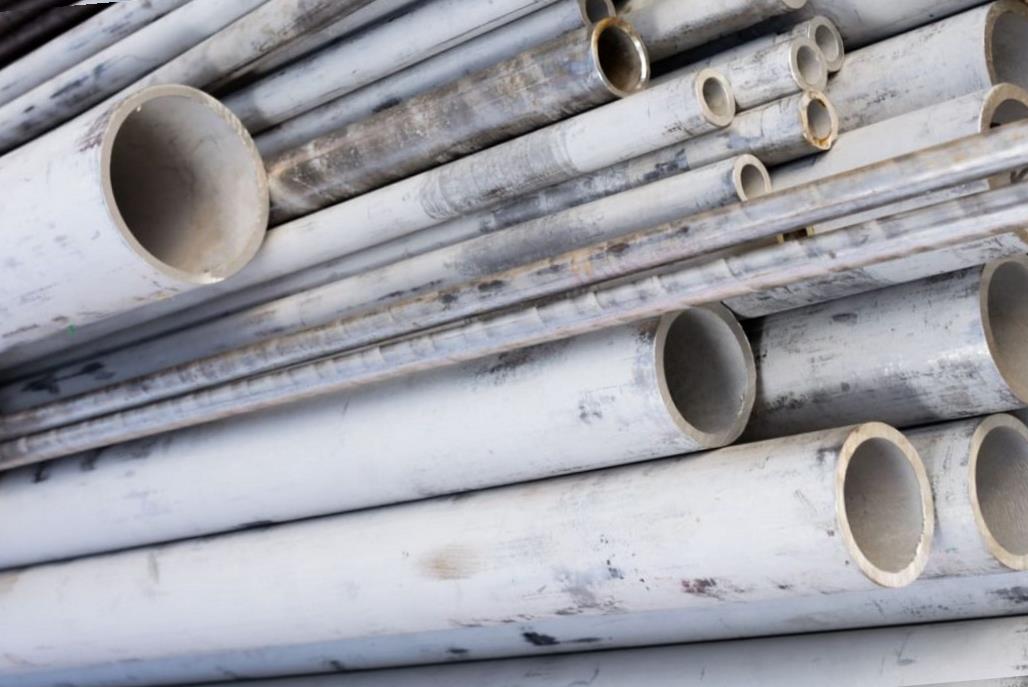
Несмотря на множество различных материалов с различными характеристиками, три группы выделены стандартом ГОСТ 5632-72, что отражено в служебных названиях, помогающих определить область их использования.
- Я обладаю свойством коррозионной стойкости, то есть я способен противостоять любым формам коррозии, включая электрохимическую и коррозию под напряжением.
- II - Термоустойчивые и устойчивые к окислению: обладают устойчивостью к вредным факторам и процессу образования оксидов при температуре свыше 550⁰. Применяются при производстве ненагруженных элементов.
- III - Термостойкие: способны выдерживать механические нагрузки при высоких температурах.
Все стали с высоким содержанием легирующих элементов разработаны для использования в сложных условиях. Примеры:
- Криогенные стали: 10Х14Г14Н4Т и 12Х18Н10Т.
- Сопротивляющиеся воздействию кислот: 08Х17Н5М3, 06ХН28МДТ, ХН65МВ.
- Такие как 20Х17Н2 и 95Х18 относятся к сталям высокой прочности.
- Для структур, расположенных в жестких условиях, используются следующие материалы: 08Х21Н6М2Т и 10Х17Н13М2Т.
- Относительно судостроения на море: 07Х16Н4Б и 09Х17Н7Ю1.
- Следующие сплавы используются в бытовых предметах: 12Х17, 08Х18Т1, 10Х14Г14Н3.
- Изделия, которые подвергаются ударным нагрузкам, обычно изготавливаются из таких материалов, как 20Х13 или 25Х13Н2.
- Материалы, подлежащие обработке: 30Х13, 40Х13.
- Турбины оборудуются материалами, такими как ХН60Ю и ХН77ТЮРУ.
- Оборудование для печей и выхлопных систем изготавливается из материалов 36Х18Н25С2 и ХН45Ю.
Некоторые бренды могут найти применение в различных областях. Например, 12Х18Н10Т может работать в температурных интервалах от -196 до +600 градусов Цельсия. Он также служит надежным строительным материалом для производства деталей, которые подвергаются высоким нагрузкам, и противодействует воздействию кислот, щелочей и солей. Кроме того, этот материал можно сваривать без каких-либо ограничений.
Группа жаропрочных сплавов включает в себя значительное количество хрома (не менее 28%) и кремния. В ходе окисления, эти элементы образуют защитный слой окислов, который предохраняет поверхность от разрушений. Такие сплавы применяют в производстве установок для пиролиза, теплообменников, термопар и электродов. К примерам таких сплавов относятся 15Х25Т и 40Х10СМ2.
Композиции, обладающие жаропрочностью, склонны к дополнительному упрочнению благодаря образованию дисперсных частиц под воздействием температуры. В состоянии перенасыщения атомы, которые не находятся в связи с кристаллической решеткой, перемещаются к границам зерен, формируя включения. Известно три вида такого упрочнения: карбидное, интерметаллидное и смешанное.
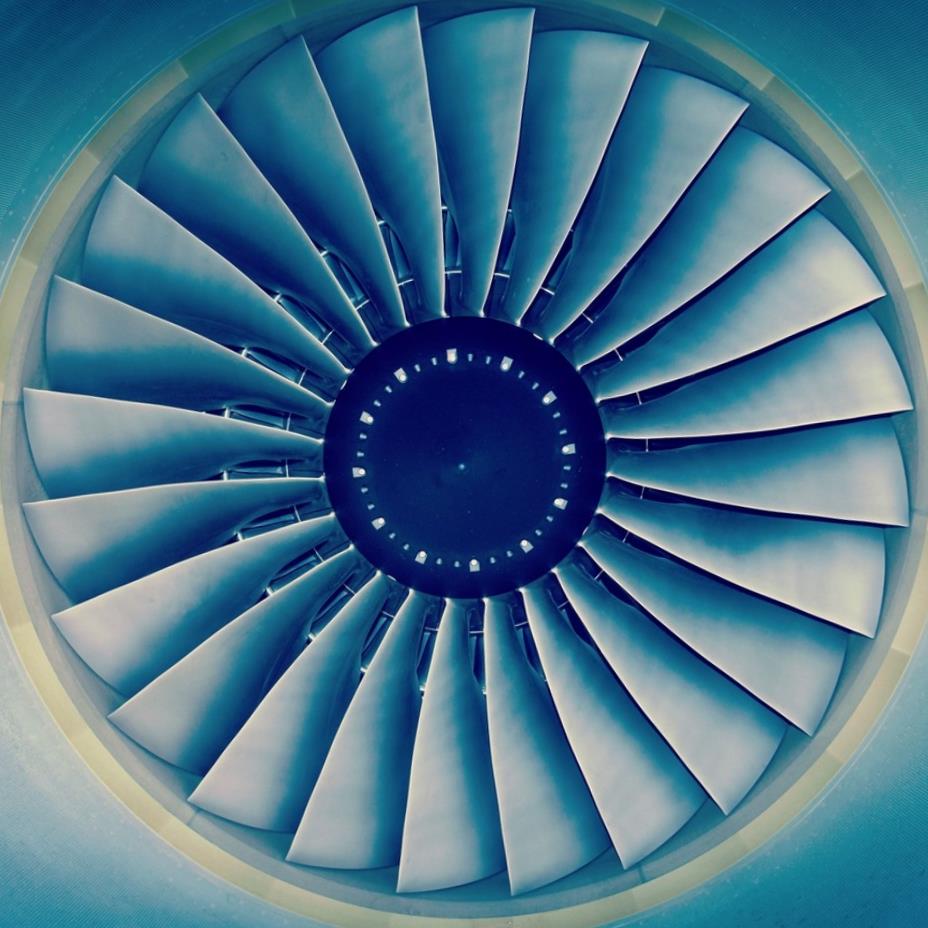
Устойчивость к агрессивным окружающим условиям, рабочим температурным режимам и нагрузкам определяется структурными особенностями и формированием кристаллического скелета. В соответствии с этими факторами осуществляется распределение сплавов по различным категориям.
- Ферриты, обладающие пластичностью и зернистостью в своей неоднородной структуре, имеют сниженную устойчивость к коррозии. Это связано с тем, что железо, участвующее в карбидных соединениях, реагирует на повышенные уровни агрессивных субстанций. Вместе с тем, упорядоченная кристаллическая решетка обеспечивает сохранение магнитной проницаемости.
- Аустениты обозначают промежуточное состояние при остывании расплава, однако сплавы, основанные на хром-никель-марганцевой системе, способны удерживать его в нормальных условиях. Их характеризуют отличными антикоррозийными свойствами и хорошей подверженностью обработке под давлением.
- Мартенситы формируются в хромовых соединениях при быстрой заморозке аустенитов. Металл становится компактным, устойчивым к холодному хрупкости, приобретает повышенную устойчивость и развивает способность восстановления после небольших повреждений. Мартенситы устойчивы к окислению при экстремальном нагреве, но их использование обычно ограничено при взаимодействии с окислителями в связи с тенденцией к межкристаллической коррозии.
Часто присутствие большого числа добавок приводит к образованию двух фаз одновременно, которые отличаются своими свойствами. Среди видов с высоким содержанием легирующих элементов можно выделить следующие:
- Включения мартенсита и частицы, отвечающие за дисперсное упрочнение, обеспечивают увеличенную прочность аустенитно-мартенситной стали, независимо от их соотношения.
- В составе мартенситно-ферритных материалов, где феррит присутствует до 10%, находятся хромистые соединения, которые обеспечивают необходимую пассивацию поверхности и соответствующую твердость. Этот вид материала широко используется в процессе изготовления нефтехимического оборудования. Однако стоит учесть, что при сварке есть большой риск появления хрупких трещин.
- До 10% феррита в аустенитно-ферритной структуре способствует улучшению механической прочности по сравнению с аустенитными. Степень коррозионной устойчивости определяется химическим формулами. Аустенитная решетка подвержена коррозии при воздействии хлора, но в случае сочетания фаз, эту проблему можно решить.
Стали аустенитного класса, богатые хромом (не менее 18%) и никелем (не менее 8%) пользуются значительным спросом. Их можно применять для большинства коррозийных сред, однако они обладают недостаточным уровнем механической прочности для создания высоконагруженных деталей и конструкций.
Процесс изготовления ферритов относительно недорог, поскольку не предполагает применения дорогих ингредиентов или сложной термической обработки для модификации молекулярной структуры. Разработка дуплексных структур обеспечивает новые преимущества в решении технологических вопросов, они часто превосходят по характеристикам определенные типы или обладают более высокими экономическими показателями.
Категория сталей | Основные особенности | Марки соответствующей категории |
Мартенситные марки | Содержат углерод в приличных количествах до 0,7%, содержание хрома среднее от 8 до 19%, в незначительных количествах содержат кремний и/или марганец | 07Х16Н4Б, 13Х11Н2В2МФ, 30Х13 |
Ферритные марки | Низкое содержание углерода до 0,15%, высокое или среднее содержание хрома от 12 до 30%, в очень небольших количествах может содержать кремний, титан и/или марганец | 12Х17, 08Х13, 15Х25Т |
Аустенитные марки | Низкое содержание углерода до 0,2%, умеренное или среднее содержание хрома от 10 до 18%, никель в различных концентрациях от 3 до 25%, марганец в различных концентрациях от 1 до 14%, в небольших количествах может содержаться кремний, азот | 20Х25Н20С2, 12Х25Н16Г7АР |
Композитные мартенситно-ферритные марки | Низкое содержание углерода до 0,2%, большое или среднее содержание хрома от 10 до 16%, в небольших количествах — ванадий, марганец, кремний | 12Х13, 15Х12ВНМФ |
Композитные аустенитно-ферритные марки | Низкое содержание углерода не более 0,18%, высокое содержание хрома в среднем 23%, марганец в различных концентрациях есть сплавы как с низким содержанием 0,5%, так и с высоким содержанием 9%, возможны небольшие вкрапления кремния, алюминия, титана | 15Х18Н12С4ТЮ, 12Х21Н5Т |
Композитные аустенитно-мартенситные марки | Углерод в различных концентрациях от 0,1 до 1%, высокое содержание хрома в среднем около 16%, в небольших концентрациях — алюминий, кремний, титан | 08Х17Н6Т, 09Х15Н8Ю1 |
Маркировка
В системе маркировки России детализированно указывается химические компоненты, все элементы, которые составляют основу, а также лигатуры с концентрациями, стремящимися к 1%.
Интерпретация:
- Углеродный элемент в первой цифре представлен в виде процентных долей сотых. Так, в обозначении 12Х17 его количество составляет 0,12%.
- Символы в алфавитном формате обозначают добавленные металлы, а начальный элемент в структуре, указывающий непосредственно после углерода, является главной составляющей.
- Цифровое представление - это выражение содержимого каждого элемента в процентах. Если это значение близко или равно 1, то цифра не записывается.
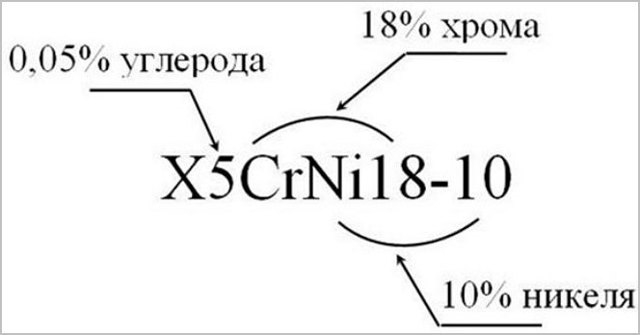
Дополнительные знаки:
- Значение "Р" в составе стали не обозначается, поскольку оно связано с процентом ванадия в составе, в то время как содержание хрома составляет всегда от 4 до 9%. Например, у стали Р9М4К8, которая является сплавом, укрепленным молибденом и кобальтом, режущие свойства.
- Состав ХН77ТЮР и ХН77ТЮРУ различается по уровню содержания углерода, что ведет к смещению пропорций в их составе.
- Методы специализированной обработки обозначаются с использованием дефиса: ПТ обозначает плазменное плавление, а ГР - процесс газокислородного рафинирования и т. д.
Обычно классификация объединяет группы, которые имеют схожие названия и характеристики. Иногда встречаются пометки вроде ЭИ827, ЭП109, которые обозначают каталог компании, занимающейся патентованием. Позже эти маркировки включаются в стандартную систему и к ним применяется общепризнанный терминологический способ обозначения.
Сварка
Запутанная взаимосвязь компонентов делает структуру уязвимой к нагреванию до температуры плавления. Во время рекристаллизации преобразуются свойства и пропорции химических веществ. В каждой ситуации метод и добавочные материалы выбираются с учетом технической документации и советов производителя.
Особенности:
- Лигатуры уменьшают теплообмен и способствуют скоплению тепла в области соединения;
- Увеличенный параметр линейного увеличения приводит к твердому связыванию свариваемых элементов и образованию трещин.
- У аустенитов наблюдаются трещины из-за высоких температур, а у мартенситов они происходят из-за низких температур.
- Утрата противокоррозийных свойств вследствие осаждения карбидов, некомплектное возобновление посредством закалки.
- Потеря пластичности является результатом стабилизации в процессе закалки сварного шва.
Применение электродов, способствующих увеличению феррита и содержащих легирующие элементы, является решением данной проблемы. В случае, если сварной шов оказывается не равномерным, в пришовной области возникают рассеянные деформации.
Выбор метода сварки осуществляется на основе теплопроводности, характеристик и веса все компонентов. Данный процесс осуществляется в условиях защитной газовой среды с начальным нагреванием и последующим быстрым охлаждением. Несмотря на то, что температура плавления некоторых видов стали может достигать 1200⁰, экстремальные температурные режимы ускоряют процессы окисления и разложения различных связей.
Некоторые типы металла не подходят для создания сварных изделий, они используются исключительно для производства клепаных деталей, обработки штамповкой или изготовления системы крепления. Если же потребуется сварка, вопрос выбора решается через выполнение расчетов. В случае сложных задач следует проводить первичные испытания.

